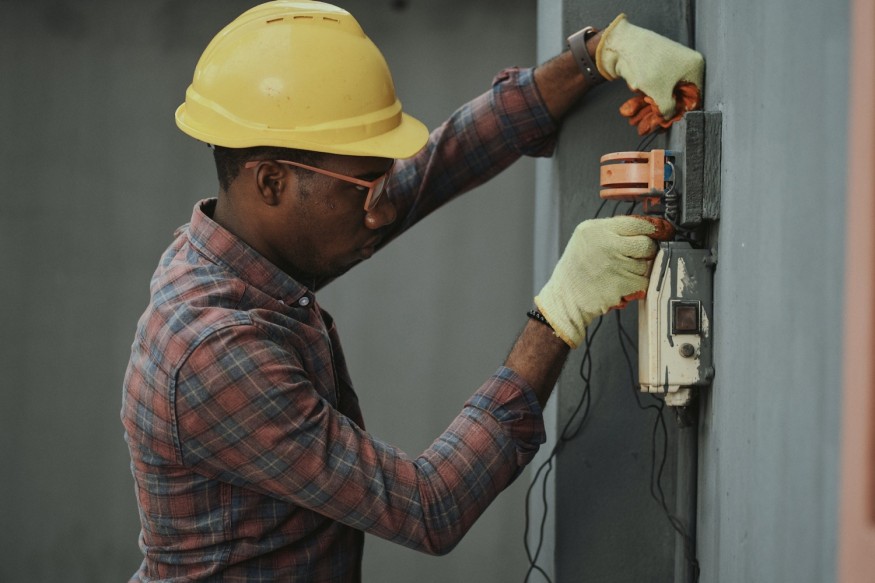
Testing and tagging is a critical process for ensuring the safety of electrical equipment. The process involves a range of tests to assess equipment safety and the application of a tag indicating its status. Below is a look into the different tests used in testing and tagging, including earth continuity testing, insulation resistance testing, and polarity testing.
It's important to note that the specific tests used in testing and tagging will vary depending on the type of equipment being tested and the requirements of the relevant regulations and standards. For example, AS/NZS 3760:2010 outlines the requirements for the in-service safety inspection and testing of electrical equipment in New Zealand and Australia. This standard specifies the types of tests that should be performed, the testing frequency and the requirements for documentation and tagging.
Earth continuity testing
Earth continuity testing is one of the most important tests used in testing and tagging. This test checks the integrity of the earth connection in electrical equipment. An effective earth connection is crucial for the safe operation of electrical equipment, as it helps to prevent the build-up of electrical charge and reduces the risk of electrical shock. Earth continuity testing involves passing a small current through the earth conductor and measuring the resistance. If the resistance is too high, it indicates a problem with the earth connection.
Insulation resistance testing
Insulation resistance testing is another critical test used in testing and tagging. This test checks the quality of the insulation in electrical equipment. Sound insulation is crucial for preventing electrical shock and reducing the risk of fires and other hazards. Insulation resistance testing involves applying a high voltage to the insulation and measuring the current that flows through it. If the current is too high, it indicates a problem with the insulation.
Polarity testing
Polarity testing is a test used to ensure that the live and neutral wires in electrical equipment are correctly connected. Polarity testing is crucial because it helps prevent electrical shock and ensures the equipment operates correctly. Polarity testing involves checking the voltage between the live and neutral wires and the voltage between the live and earth wires. If these voltages are not within the correct range, it indicates a problem with the polarity.
Load testing
Load testing involves applying a load to the equipment to ensure it can handle the rated load without overheating or failing. This test is significant for equipment that takes heavy loads, such as motors or generators. Load testing helps to ensure that the equipment can operate safely and effectively under real-world conditions. If the equipment fails the load test, it may need repair or replacement to ensure its safety and reliability.
Functional testing
Functional testing involves checking that the equipment operates correctly and meets the requirements of its intended use. This test is important for ensuring that the equipment performs its intended function and is safe to use. For example, functional testing of a power tool may involve checking that the on/off switch works correctly, that the blades rotate smoothly, and that the safety guard is in place and functioning correctly. Functional testing can also help to identify any defects or malfunctions that may affect the safety or performance of the equipment.
Visual inspection
Visual inspection is another important part of testing and tagging, as it can help to identify physical damage, signs of wear and tear, or other issues that may affect the safety of the equipment. This test involves inspecting the equipment for visible indications of damage or wear, such as cracks, dents, or frayed wires. Visual inspection can also help identify missing components, such as safety guards or protective covers. If defects or issues are identified during the visual inspection, the equipment may need to be repaired or replaced to ensure its safety and reliability.
THE takeaway
Testing and tagging power tools are important for identifying and preventing potential hazards like electrical shocks, fires, and other risks. The process involves a range of tests to assess the safety of the equipment. The specific tests used will differ depending on the type of equipment being tested and the requirements of the relevant regulations and standards.
© 2025 ScienceTimes.com All rights reserved. Do not reproduce without permission. The window to the world of Science Times.