Solar energy has been in the spotlight for years. This booming market has established itself as one of the best solutions for meeting the growing demand for electricity while reducing carbon emissions.
In this context, solar power plants deliver on their promise, producing 25 times less carbon-intensive electricity compared to a gas-fired power plant. And in any case, the share of solar power in the global energy mix is growing strongly and will continue to do so.
The key components of a photovoltaic installation are solar panels and one or more inverters, whose performance guarantees the system's productivity and efficient conversion of energy from DC to AC.
The inverter market itself is highly dynamic and competitive, with strong cost pressure. Market players constantly search for more efficient, miniaturized, and cost-optimized components.
Current sensors are an essential component of the inverter system. They are crucial to optimize the efficiency and performance of the inverter at several stages in the system. They must be efficient, reliable, and able to withstand the unexpected in even the most extreme circumstances. Integrating highly reliable current sensors capable of handling currents of up to 20 Amperes and beyond is essential to ensure stable performance, protection of the inverter, and even the whole solar installation. This is where Integrated current sensors come into play. They allow engineers in the solar inverter industry to solve the challenges of footprint, performance, and cost-effectiveness at one time.
Let's explore the key role of ICS in solar applications and what you need to bear in mind to get the best out of your solar inverter system.
Standard Solar Inverter System Description and the Essential Role of ICS in Solar Applications
Inverters are low-power systems. They can be either string inverters or micro inverters, but the system remains the same. Let's take a closer look.
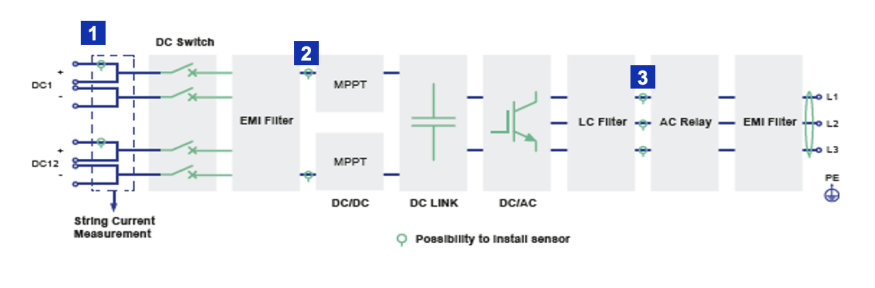
Position 1: Photovoltaic String Current Measurement
A current sensor is used to measure the current when entering the PV inverter string, with each string measuring its own current. It should also act as a protection. If a flash of lightning strikes a solar panel, it can generate a surge current (a current that comes unexpectedly, quickly, and at an extremely high magnitude).
This is where LEM's integrated current sensor HMSR SMS plays an essential role in withstanding such high electrical power to protect the solar inverter. LEM HMSR SMS is perfect for micro inverters dealing only with the current generated by one solar panel, as well as for string inverters. With its analog output, it guarantees fast signal treatment and a standard footprint to adapt to any solar system. LEM's HMSR benefits from a unique breakthrough concept with reinforced isolation technology that makes it immune to the surge current in case of lightning strike. The family has a pre-mold design to isolate the primary bar and a special footprint to allow 8mm dCp/dCI on the landing pad. The integrated micro-core inside the HMSR makes it insensitive to external magnetic fields.
With its range of cheaper, smarter, smaller current sensors capable of resisting up to 20k A current for an extra mile in safety, LEM clearly meets all technical requirements to address such massive needs.
Position 2: DC Side MPPT Current Measurement
This position is intended to maximize the system's efficiency. The current sensors need to constantly measure the current to identify the Maximum Power Point Tracking (current to maximize the efficiency of the inverter system). Here, the current rises up to 50 A but can go up to 70 A, and the system needs to add up currents for two strings.
At this stage, there is no need to have a high surge current capability since the current sensor in position 1 (PV string stage) already protects the whole system. What is more important is a fast response. In this position, LEM's integrated current sensor HMSR SMS is a perfect option that allows reaching the expected performance with a small footprint and cost-effectiveness.
For string inverters requiring a sensor with a capability > 50 A, LEM open loop sensor HLSR is the perfect fit, and the LEM ICS roadmap will bring some new exciting answers soon.
Position 3: Inverter Output AC Measurement
At this stage in the system, DC is converted into AC to feed the grid. In order to do so, the current sensor must be compliant with strict regulations. One of the most important rules is that offset cannot be injected into the grid. The regulation in place requires less than 0.25% of IPN (0.1% of IPM).
Currently, no open loops can do the job correctly, nor can an ICS. The preferred solution to tackle this is closed loops. LEM offers a range of closed-loop sensors such as LESR, LKSR, CKSR, etc.
And again, LEM R&D teams have some news in the ICS to better tackle this challenge.
LEM — A trusted partner for performing string and micro inverters
In a very dynamic market driven by booming global demand for 100% green energy, photovoltaic inverter suppliers face an increasingly competitive marketplace where cost pressure is high.
In terms of technology, the trend is already towards three-phase low power. This trend is set to grow, and the pressure on component prices will continue in the future.
LEM's engineers and R&D teams have perfectly understood customer needs to provide the best possible equipment at an ever more optimized cost tailored to all photovoltaic requirements.
LEM's range of ICS and what is in the roadmap for future launches brings solutions to square the circle of combining increasing performance with lower cost and a smaller footprint.
© 2025 ScienceTimes.com All rights reserved. Do not reproduce without permission. The window to the world of Science Times.