A new generation of robots developed with intelligence and flexibility was recently invented for warehouse use.
As COVID-19 stresses worldwide supply chains, the logistics field has been working to help keep workers safe and enhance their efficacy, IEEE Spectrum reported.
Nevertheless, there are several warehouse operations that do not lend themselves to customary automation, such as tasks where both the inputs and outputs of a process are not always well-defined, not to mention, cannot be fully regulated.
A primary example is this new Boston Dynamics robot called Stretch that can move heavy boxes where they should go as fast as an experienced worker at a warehouse.
ALSO READ: This 3D Bionic Skin Can Convey Robots To Feel The Sensitivity Of Various Environment
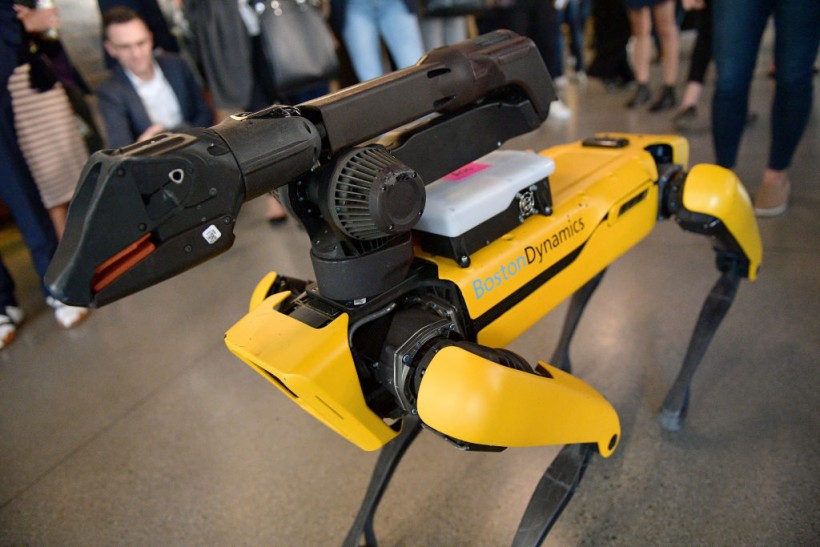
Boston Dynamics' SpotMini Robot on display at WIRED25 Summit: WIRED Celebrates 25th Anniversary With Tech Icons Of The Past & Future on October 15, 2018, in San Francisco, California.
The Ability to Move 50-Pound Boxes
Stretch was designed differently from Boston Dynamics' humanoid and quadrupedal robots Atlas and Spot, according to Robots Science.
It has a single massive arm, a gripper packed with sensors and an array of suction cups and an omnidirectional mobile base. The developers designed the new robot with the ability to transfer boxes weighing as heavy as 50 pounds from the back of a truck to the belt of a surveyor at an 800-boxes-per-hour rate.
In a regular scenario, an experienced human worker can move boxes at the same rate but not with a whole-day duration. Meanwhile, Stretch can work up to 16 hours before battery recharging.
The job is heavy and can be risky for humans, specifically when the boxes need to be moved from near the ceiling or floor of the trailer.
Doing the Hardest Job
According to senior vice president for warehouse robotics Kevin Blankespoor at Boston Dynamics, truck unloading is among the most challenging jobs in a warehouse, and that is one of the reasons "we're starting there with Stretch."
However, the company executive explained that Stretch is not designed as a total replacement for its workforce. The idea is that several Stretch robots could make a human worker an order of magnitude more effective.
Usually, there'll be two people uploading every truck and that will be unnecessary with Stretch. The human workforce will still need to unload the boxes from four to five trucks and use Stretch robots as tools.
All this robot needs is to be shown a trailer's back full of boxes, and it will automatically go to work by placing each box on a conveyor belt one after another until the trailer becomes empty.
Robot Supervision
People are still there to guarantee that everything is going smoothly, and they can step in if Stretch is running into something that it cannot handle. However, their full-time job turns out to be robot supervision rather than lifting heavy boxes all day.
Attaining this level of dependable autonomy with Stretch has taken the company years of work and decades of experience assembling robots that are robust, agile, and fast.
Other than the challenge of inventing a high-performance robotic arm, the firm still needs to solve some problems that people consider trivial but difficult for the robots - for instance, looking at a wall of closely packed boxes and being able to tell if one is stopping and another starts.
Information about Stretch, the robot, is shown on Boston Dynamics' YouTube video below:
RELATED ARTICLE: Fabricated Electronic Skin Perceive Pain Like Humans, Paving Way for Prosthetics and Robotics
Check out more news and information on Robotics in Science Times.