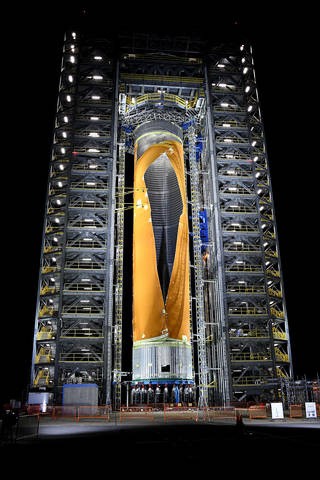
Last Dec 5, the National Aeronautics and Space Administration (NASA) placed the Space Launch System rocket under extreme tests for the engineers to figure out how much stress it will have to undergo to reach its breaking point.
WHAT IS UNIQUE ABOUT NASA'S SPACE LAUNCH SYSTEM ROCKET?
Conveniently called the SLS, NASA's Space Launch System rocket is the most advanced launching vehicles that the agency built and is specifically designed to provide a foundation for human exploration beyond the planet (READ: NASA Curator Plans for Manned Mission to the Moon).
NASA's Space Launch System rocket aims to launch astronauts to deep space missions and its first gig is to send astronauts and large cargo to the Moon via the Orion spacecraft (READ: Super Guppy Transports Orion Spacecraft to NASA's Plum Brook Station for Testing). The SLS rocket will catapult Orion to the Moon by providing the much-needed speed for the spacecraft. According to the agency's press release, NASA's Space Launch System rocket is flexible and can carry robotic scientific missions to the Moon, Mars, and beyond.
Last weekend, the engineers behind NASA's Space Launch System rocket tested the vehicle and placed it under extreme conditions to figure out how long can it withstand environments harsher than what it is designed for. For instance, the liquid hydrogen tank inside NASA's Space Launch System rocket was able to withstand more than 260% of expected flight loads over five hours.
In a press release issued by the agency, chief engineer Neil Otte explains, "we purposely took this tank to its extreme limits and broke it because pushing systems to the point of failure gives us additional data to help us build rockets intelligently. We will be flying the Space Launch System in the decades to come and breaking the propellant tank today will help us safely and efficiently evolve the SLS rocket."
The liquid hydrogen tank inside NASA's Space Launch System rocket was also able to pass its earlier tests including being able to withstand forces expected at engine thrust levels that are specifically planned for the Artemis missions to the Moon. The tank showed no signs of cracking and buckling.
HOW DID THE ENGINEERS TEST NASA'S SPACE LAUNCH SYSTEM ROCKET?
Engineers behind NASA's Space Launch System rocket conducted the tests by combining gaseous nitrogen for pressure and hydraulics for loads, meaning, with this methodology, the engineers are exposing the liquid hydrogen tank to higher forces which the engineers predicted to cause a malfunction in the rocket.
The liquid hydrogen tank was able to pass the same test done at the Marshall Space Flight Center. According to Mike Nichols, Marshall Space Flight Center's lead test engineer, this final tank test marks the largest controlled test-to-failure done to a rocket's pressurized tank and that the data from this experiment shall benefit aerospace companies that design rocket tanks.
The engineers -- both from NASA and from Boeing -- also simulated liftoff and flight to a liquid hydrogen tank that is quite similar to a flight tank. They used large hydraulic pistons that can deliver millions of pounds-worth of compression, tension, and bending forces. To be able to measure the stress, pressure, and temperature, thousands of sensors are installed in the test tank as well as high-speed cameras and microphones. Boeing's qualification test manager Luke Denney explains, "the initial tank buckling failure occurred at the same relative location as predicted by the Boeing analysis team and initiated within 3% of the predicted failure load. The accuracy of these predictions against real-life testing validates our structural models and provides high confidence in the tank design."
© 2025 ScienceTimes.com All rights reserved. Do not reproduce without permission. The window to the world of Science Times.