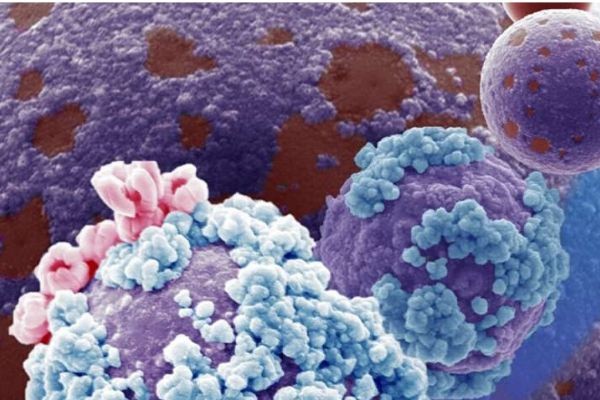
A materials engineering lab at Iowa State University has developed a transforming metal that changed its surface when subjected to heat. The metallic substance has a liquid state and quite possibly a solid when transformed due to external heat sources.
When particles of the liquid metal alloy react when heated, causing the change from smooth to rough are nanowires and spheres on the surface. This already featured and published in the Angewandte Chemie journal. The engineers reported their findings in the journal to explain how it was done.
One of the engineers is Martin Thuo, whose major is materials science and engineering, the main researcher. By manipulating the heat applied to the allow, its surface patterns will be controllable too. Heat as the main agent causes changes in the molecular structure of the metal as observed.
This technology might be the first of alloys that are "smart" and customized for a variety of patterns, depending on the application. Varying the heat or stimulus applied to the liquid/solid phase metal from sensing to catalysis. Thou and his co-researchers wrote this finding when testing the transforming metal.
Before getting these dramatic results from their testing, metal alloys used were gallium, indium, and tin particles with an oxide shell that is chemically stable as well. Changes in the allow as they are heated, causes the surface to get rougher, harden, and is almost like a solid alloy in this state.
The liquid metal will climb to the top surface because of heating. First to climb to the surface is gallium, and indium rises because it melts with more heat. The last is the tin particles that are affected by 1,600 degrees-Fahrenheit, making tin needing the most heat in the layers.
The process of how the liquid/solid allow works is by "continuously changing its composition when the heat is applied". Movement of liquid metals rising from the bottom to the top part of the alloy surface. All this is done by manipulating and adjusting the heat applied to the alloy.
An alloy undergoes a shift with its structure, based on the amount heat energy applied is cutting edge stuff. Similar to an "alloy Chameleon", except the alloy is altering itself based on the heat. When developed for future use, especially the application of heat transformable metals.
Winnie Kiarie explained that the metal alloys are studied in a precisely controlled environment, to control all variables of the experiments. By, keeping tabs on time, temperature and oxygen levels gives better control of what happens to the chameleon alloy.
Another factor that is included, in highly controlled environments, is the ability to guess and to program the alloy surface. One of the promising applications is to fine-tune how the metal acts as a catalyst or to absorb other compounds. Another aspect is that transforming metals will be compatible with metal alloys.
Transforming metals reacting to heat is not one of a kind. Most metals are the same, except this has a liquid and solid phase and it is a common property as well. When fully developed, this smart metal will be very useful with its shifting qualities.
Related Article: Engineers develop 'chameleon metals' that change surfaces in response to heat
© 2025 ScienceTimes.com All rights reserved. Do not reproduce without permission. The window to the world of Science Times.