Researchers have devised a new process that efficiently converts waste from rubber tires into graphene, which in turn could be used to reinforce concrete.
A team from Rice University in Houston, Texas is behind the new technology that could make for stronger roads at reduced costs. According to chemist James Tour from Rice University's Department of Chemistry, the environmental benefits of infusing concrete with graphene are "clear."
"Concrete is the most-produced material in the world, and simply making it produces as much as 9% of the world's carbon dioxide emissions," Tour said in a press release from Rice. "If we can use less concrete in our roads, buildings, and bridges, we can eliminate some of the emissions at the very start."
Researchers report the new technique in an article "Flash Graphene from Rubber Waste" published in the latest journal Carbon.
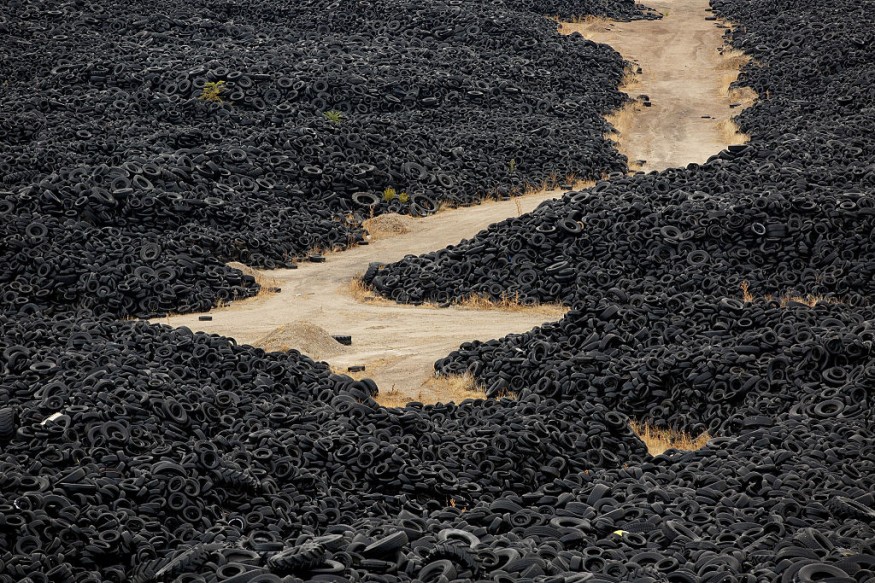
ALSO READ : Scientists Create Bendable Concrete and Carbon-Infused Cement Mixes to Curb Carbon Emissions
New Method For Extracting Graphene
Researchers, in the abstract for their report, note how most of the existing production processes for graphene are "time-consuming, solvent-intensive, and energetically demanding." This led them to turn to flash Joule heating, a process that promises to work around existing limitations in synthesizing graphene.
By controlling parameters like pulse voltage and pulse time in their setup, researchers were able to extract turbostratic flash graphene (tFG) from rubber waste. They were later able to verify the process through the use of Raman spectroscopy, X-ray diffraction, and thermogravimetric analysis. Furthermore, the produced graphene is notably easier to exfoliate and disperse into various solvents thanks to its turbostratic arrangement. This means that the multilayer graphene material is electronically decoupled because of interlayer rotation, making the multilayer material behave as one single layer.
The flash process used in creating tFG has been previously introduced by Tour and his colleagues to convert food waste, plastic, and other carbon sources by exposing them to electricity that removes everything, leaving carbon atoms in the samples. Then, the carbon atoms assemble into turbostratic graphene.
More Challenging Material
Researchers admit that rubber is more challenging as a graphene material compared to food or plastics. They were able to optimize the process by testing out commercial pyrolyzed waste rubber from tires. After extracting useful oils from these waste tires, the carbon residue they recovered had had near-zero value before they used it in their new method.
The turbostratic flash graphene recovered about 70 percent of the material from tire-derived carbon black. When they flashed, the shredded rubber tires mixed with plain carbon black for increased conductivity yielded 47 percent graphene. The controlled electrical pulses in the experiment ranged from 300 milliseconds to 1 second, with the electricity used in the conversation process factored in by the researchers for the costing - estimating about $100 for every ton of starting carbon.
For the next step of their study, they mixed small amounts of tire-derived graphene - about 0.1 weight/ percent for tire carbon black and weight/ percent for carbon black and shredded tires - with Portland cement to use in producing concrete cylinders. The concrete was then left to cure for an entire week before testing its strength. Researchers found out that the concrete cylinders were 30 percent more durable in terms of compressive strength.
RELATED ARTICLE : Rare Mineral of Roman Concrete Found in Japanese Nuclear Power Plant
Check out more news and information on Concrete in Science Times.
© 2025 ScienceTimes.com All rights reserved. Do not reproduce without permission. The window to the world of Science Times.