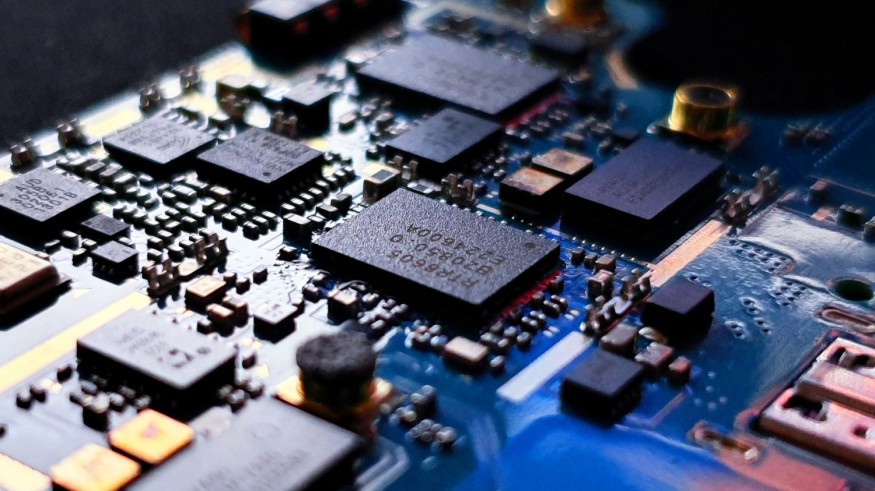
Discover the essential roles and manufacturing processes of sheet metal components in electronics. Learn how these components are vital for modern electronic devices. Find expert insights and a comprehensive outline here.
In the complex world of electronics, sheet metal parts are crucial in forming the gadgets we use every day. These parts are the unsung heroes of smartphones and laptops, providing structural integrity, heat dissipation, electromagnetic shielding, and more.
This article dives deep into the key roles these components play in electronics and unveils the manufacturing processes that bring them to life.
What is sheet metal fabrication for electronics?
Sheet metal fabrication for electronics is a specialized process that involves manipulating metal sheets, typically of materials like aluminum, steel, or copper, to produce components integral to electronic devices. This method involves various techniques, including cutting, bending, and assembling, tailored to the intricate demands of electronic applications.
As technology continues to advance and the demand for more compact, efficient, and sophisticated electronic devices grows, the need for precision in component manufacturing becomes paramount. Here, rapid sheet metal fabrication comes into play. This advanced approach allows for faster turnaround times without compromising on the quality or precision of the components. By leveraging rapid sheet metal fabrication, manufacturers can accelerate production cycles and adapt swiftly to industry innovations.
The versatility of sheet metal fabrication ensures that electronic products are both robust and optimally designed. Components such as casings, connectors, and heat sinks, which are crucial for the functionality and efficiency of electronic devices, often owe their existence to these fabrication techniques. With the merging of traditional craftsmanship and modern rapid fabrication methods, the electronics industry is poised to meet the evolving needs of today's consumers.
Manufacturing Process: From Raw Material to Finished Component
The journey of sheet metal components from raw material to finished product involves several intricate steps. Let's explore the manufacturing process that brings these essential components to life.
Material Selection
The process begins with material selection. Various metals, such as aluminum, stainless steel, and copper, are chosen based on factors like conductivity, strength, and corrosion resistance.
Cutting and Shearing
Sheets of chosen metal are cut into desired shapes using advanced cutting techniques such as laser cutting, waterjet cutting, or traditional shearing.
Forming and Bending
Forming machines apply precise pressure to bend the metal sheets into the required shapes, creating complex geometries for sheet metal enclosures, heat sinks, and connectors.
Stamping and Punching
Stamping and punching machines create patterns, holes, and detailed designs on metal sheets, enhancing functionality and aesthetics.
Joining and Welding
Various joining techniques, including spot welding, TIG welding, and brazing, are employed to assemble different components into a cohesive unit.
Surface Treatment
Surface treatments like painting, powder coating, anodizing, and plating provide protection against corrosion, enhance aesthetics, and improve conductivity.
Quality Control
Stringent quality control measures, including dimensional checks, stress tests, and visual inspections, ensure the final components meet industry standards.
Sheet Metal Components: The Backbone of Electronics
Sheet metal components form the foundation of many electronic devices, supporting their functionality and aesthetics. These components offer vital roles that contribute to the overall performance of electronics.
Structural Integrity and Enclosures
Sheet metal enclosures provide protection for delicate internal components against physical damage, dust, and moisture. These enclosures ensure the longevity of devices, making them durable for everyday use.
Heat Dissipation
Electronics generate heat during operation, which can adversely affect performance and lifespan. Sheet metal heat sinks efficiently dissipate heat, maintaining optimal operating temperatures and preventing overheating.
Electromagnetic Shielding
In our interconnected world, electromagnetic interference (EMI) can disrupt electronic devices. Sheet metal components with proper shielding prevent unwanted electromagnetic radiation, enhancing device reliability.
Connectors and Mounting
Sheet metal connectors facilitate electrical connections between components, ensuring seamless communication within devices. Additionally, these components provide secure mounting points for various internal parts.
Aesthetics and Design
Beyond functionality, sheet metal components contribute to the visual appeal of electronic devices. Precise manufacturing processes allow for intricate designs and seamless integration into the device's overall look.
Conclusion
In summary, sheet metal components stand as vital cornerstones within the realm of the electronics sector, significantly enhancing the operational capabilities, longevity, and visual appeal of contemporary devices.
Acting as steadfast guardians, these components undertake pivotal tasks, ranging from bolstering structural resilience to orchestrating efficient heat dispersion and safeguarding against electromagnetic interference. It is these unsung champions that orchestrate the seamless performance of our electronic companions.
Gaining insight into the intricate intricacies of the manufacturing procedures that birth these components instills within us a heightened admiration for the meticulous artistry and engineering mastery embedded in each electronic marvel we engage with.
FAQs
What are the primary roles of sheet metal components in electronics?
Sheet metal components in electronics serve roles such as providing structural integrity, heat dissipation, electromagnetic shielding, and connectors.
How do sheet metal components prevent electromagnetic interference?
Sheet metal components with proper shielding materials create a barrier that prevents electromagnetic radiation from interfering with device functionality.
What metals are commonly used for manufacturing sheet metal components?
Due to their conductivity and durability, aluminum, stainless steel, and copper are among the most commonly used metals for sheet metal components.
How do sheet metal heat sinks work?
Sheet metal heat sinks dissipate heat through their large surface area, allowing the heat to transfer away from the electronic components and into the surrounding environment.
What is the significance of surface treatments on sheet metal components?
Surface treatments like plating and anodizing protect sheet metal components from corrosion and enhance their visual appeal, extending their lifespan.
How do sheet metal connectors facilitate device functionality?
Sheet metal connectors establish electrical connections between different components within an electronic device, enabling seamless communication and operation.
© 2025 ScienceTimes.com All rights reserved. Do not reproduce without permission. The window to the world of Science Times.