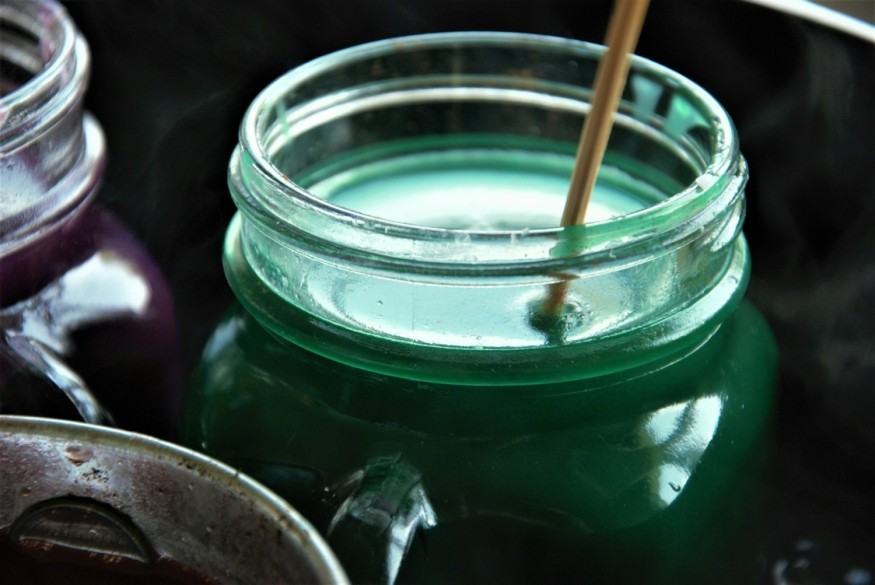
Introduction
The lost wax casting process, also known as investment casting, is a time-honored technique that has been used for thousands of years to create precise and intricate metal components. This method involves creating a wax model of the desired object, which is then encased in a ceramic material to form a mold. Once the mold is heated, the wax melts away, leaving a hollow cavity into which molten metal is poured to form the final cast object.
Despite its ancient origins, the lost wax casting method remains a cornerstone in modern prototyping and manufacturing. Its relevance has only grown with advancements in technology, such as 3D printing, which has revolutionized how wax models are created. The precision and versatility of lost wax casting make it particularly valuable for industries requiring detailed and complex designs, including aerospace, jewelry, art, and particularly in medical technology, where bespoke, perfectly tailored components are often necessary.
The enduring significance of this casting method lies in its ability to produce high-quality, complex shapes with excellent surface finishes and tight tolerances. It is this capability that makes lost wax casting an indispensable tool in the modern manufacturing toolkit, bridging the gap between ancient craft and contemporary manufacturing needs.
Advantages of Lost Wax Casting for Prototypes
Lost wax casting is renowned for its precision and versatility, particularly beneficial for producing complex prototype models that other manufacturing techniques might struggle to replicate. Here's how lost wax casting stands out in the realm of prototype development:
Precision and Detail: One of the most compelling advantages of lost wax casting is its extraordinary precision. This method can produce components with intricate details and undercuts that might be impossible through traditional machining or die casting. The accuracy of the wax model, which is the blueprint for the final product, ensures that even the smallest features are faithfully replicated in the final metal part.
Versatility in Materials: Lost wax casting is not limited to a specific type of metal, which makes it highly versatile for various industrial applications. It can be used with a wide range of metals and alloys, including stainless steel, aluminum, bronze, and precious metals. This flexibility allows designers and engineers to experiment with different materials to find the optimal combination of properties for their prototype.
Surface Finish and Integrity: The surface finish achieved with lost wax casting is superior to many other casting methods. Since the molten metal is poured into a smooth ceramic mold, the final product often requires minimal finishing work. This quality is particularly important for prototypes that need to be evaluated for their aesthetic attributes in addition to their functional characteristics.
Efficiency and Cost-Effectiveness for Small Runs: While lost wax casting can be more labor-intensive than some modern methods, it remains cost-effective for small production runs. The process does not require expensive molds or tooling, making it ideal for prototypes and limited edition items where the initial investment needs to be kept low.
Comparison with Other Prototyping Techniques:
Compared to techniques like 3D printing, CNC machining, and injection molding, lost wax casting offers unique benefits that make it suitable for specific scenarios:
- 3D Printing: Although 3D printing is excellent for rapid prototyping with plastics and some metals, lost wax casting surpasses it when high-quality metal prototypes are required. The strength and finish of cast metals are often superior, and the material properties are better suited for functional testing.
- CNC Machining: CNC machining provides great accuracy and can work with a broad range of materials. However, it can be wasteful as the material is removed from a solid block; lost wax casting is additive, making it more material-efficient for complex shapes.
- Injection Molding: This method is efficient for high-volume production but involves high initial costs for creating molds. For metal prototypes and low-volume runs, lost wax casting is often more feasible and economical.
In summary, lost wax casting holds a significant edge in creating high-fidelity, complex prototypes, especially when the intricacy of design, material properties, and surface quality are paramount. Its ability to combine detail, material diversity, and cost-effectiveness makes it an essential prototyping tool in industries where precision and versatility are critical.
Materials Needed for Lost Wax Casting
The lost wax casting process requires specific materials and tools to create detailed and high-quality prototypes. Understanding what is needed at each stage of the process is essential for anyone looking to utilize this method. Here's a comprehensive breakdown of the materials and tools required for lost wax casting:
Materials:
- Wax: The first and most crucial material in lost wax casting is the wax used to create the original model. This model will eventually be cast in metal. The wax should be malleable yet stable enough to handle without distorting the intricate details of the design. There are various types of casting waxes available, including hard waxes for sharper detail and softer waxes for larger pieces with smoother surfaces.
- Investment Material: After the wax model is created, it is encased in an investment material that forms the mold. This material needs to be able to withstand high temperatures without cracking or reacting with the metal. The most common investment used is a mixture of plaster and silica, which provides a smooth surface finish on the final metal product.
- Metal: The choice of metal depends on the prototype's requirements in terms of strength, durability, and aesthetic qualities. Common metals used in lost wax casting include bronze, aluminum, steel, silver, and gold. Each metal has its melting point and specific handling requirements.
Tools and Equipment:
- Wax Melter: To begin the process, you'll need a mechanism to melt the wax. A wax melter or a simple double boiler can serve this purpose.
- Mold-Making Frames or Flasks: These containers hold the investment material and wax model during the setting and curing phase.
- Kiln: A kiln is critical for two reasons—melting out the wax and hardening the investment mold. The kiln needs to reach temperatures high enough to burn away the wax completely without damaging the mold.
- Crucible and Metal Melting Furnace: Once the wax is removed, the next step is melting the metal to be cast. A crucible is used to hold the metal inside the furnace until it reaches the necessary temperature.
- Casting Machine: Depending on the complexity and size of the pieces, a casting machine might be used to ensure the molten metal is injected into every crevice of the mold. Vacuum, centrifugal, or pressure-casting machines are common choices.
- Finishing Tools: Once the metal has cooled and been removed from the mold, various tools are needed to clean up and finish the surface. These might include files, grinders, polishers, and engraving tools to refine the details and achieve the desired finish on the prototype.
- Safety Equipment: Safety is paramount when dealing with high temperatures and molten metal. Protective gear such as heat-resistant gloves, face shields, and aprons are essential.
Understanding and gathering these materials and tools is the first step toward mastering the lost wax casting process, allowing for the production of precise and complex metal prototypes. Whether you're working in a professional foundry or setting up a small workshop, ensuring you have the right supplies is crucial for successful casting outcomes.
Step-by-Step Guide to Creating Complex Prototypes Using the Lost Wax Method
Creating complex prototypes through lost wax casting involves meticulous planning and execution. This step-by-step guide will take you through the entire process, from design to the final product.
Designing the Prototype
- Conceptualizing and Designing the Model: Begin by conceptualizing the prototype you wish to create. This involves sketching out designs and considering the functionality and aesthetics of the final product. Use computer-aided design (CAD) software to create precise digital models. These models can then be modified to ensure manufacturability in the casting process, such as adding sprues and gates for metal flow.
- Considerations for Manufacturability and Casting: It's crucial to consider factors such as draft angles, wall thickness, and undercuts, which affect the mold's ability to properly form and release the final metal cast. Simplify complex areas and ensure that details are not too fine to be captured by the investment material.
Model Creation
- Methods for Sculpting or 3D Printing the Wax Model: You can create the wax model either by traditional sculpting or by using modern 3D printing technology. 3D printing is particularly beneficial for intricate designs as it can produce highly accurate and repeatable models.
- Achieving High Precision and Resolution in the Wax Model: Ensure the wax model is smooth and free of any defects, as imperfections can transfer to the final casting. High-resolution 3D printers and quality wax materials can be used to capture fine details without causing issues during the mold-making process.
Creating the Mold
- Encasing the Wax Model in a Ceramic Shell or Investment Mold: Carefully encase the wax model in a ceramic shell or plaster-based investment. This involves dipping the model in a ceramic slurry followed by strewing or sprinkling with stucco material and allowing each layer to dry thoroughly to build a robust mold.
- Techniques for Ensuring a Flawless Mold Surface: Avoid air bubbles and ensure the surface is smooth and even. This might require vibrating the mold or using a vacuum chamber during the pouring of the investment material to pull air out and ensure a dense, even coating.
Wax Removal
- Process of Melting Out the Wax (Lost Wax): Heat the mold in a kiln to melt and burn out the wax. This stage is critical and must be controlled carefully to ensure all wax is removed, leaving a clean, empty mold cavity.
- Ensuring Complete Wax Elimination from the Mold: Verify that all wax residues are eliminated to prevent defects in the metal cast. This might involve multiple heating cycles and inspections.
Casting the Metal
- Preparing the Metal for Casting: Choose the appropriate metal based on the prototype's requirements and melt it in a crucible until it reaches the correct pouring temperature.
- Pouring the Metal into the Mold and Considerations for Different Metals: Pour the molten metal into the hot mold, taking into consideration the metal's temperature and properties, which can affect how it fills the mold and solidifies.
Finishing the Prototype
- Techniques for Removing the Investment Mold: Once the metal has cooled and solidified, carefully break away the ceramic shell or investment material to reveal the cast metal part.
- Cleaning and Finishing the Metal Prototype: Clean the metal prototype to remove any residues or scales formed during casting. Techniques like sandblasting, polishing, and machining may be employed to achieve the desired surface finish.
- Inspection and Quality Control Measures: Finally, inspect the prototype for any defects or discrepancies in dimensions and perform any necessary reworks. Quality control ensures the prototype meets all specifications and functional requirements.
This methodical approach to lost wax casting allows for the creation of complex, high-quality prototypes that meet precise engineering and design specifications.
Troubleshooting Common Issues in Lost Wax Casting
Lost wax casting, while highly effective for creating detailed and complex parts, can encounter several issues that may affect the final quality of the prototypes. Understanding these common problems and knowing how to address them is crucial for ensuring the success of your casting projects. Here are solutions for typical issues and tips for maintaining dimensional accuracy and surface quality.
1. Incomplete Wax Removal:
- Problem: Residual wax in the mold can lead to defects in the metal cast, such as porosity or incomplete sections.
- Solution: Ensure that the kiln reaches the appropriate temperature and maintain it for sufficient time to burn out the wax completely. Consider using a steam dewaxing unit before the burnout to remove most of the wax.
2. Cracks in the Investment Mold:
- Problem: If the ceramic shell or investment cracks, metal can leak during casting, causing a failed cast or requiring extensive cleanup.
- Solution: Control the drying and curing stages of the mold carefully. Ensure that each layer of the investment is completely dry before applying the next. Avoid rapid changes in temperature during the heating and cooling phases to minimize thermal stress.
3. Air Entrapment:
- Problem: Air bubbles can form and become trapped in the mold, leading to surface irregularities or internal voids.
- Solution: Vibrate the mold slightly after pouring the investment to help air bubbles rise to the surface. You can also use a vacuum or pressure during the investment pouring process to force air out and ensure a dense, even mold.
4. Metal Shrinkage and Misruns:
- Problem: Metal may shrink as it cools, leading to dimensional inaccuracies or thin sections not filling completely.
- Solution: Design the mold with proper sprues, gates, and risers to ensure adequate flow and feeding of molten metal. Consider the shrinkage properties of the metal being used and adjust the mold design accordingly.
5. Rough Surface Finish:
- Problem: The final casting may have a rough surface, which could be due to several factors, including the quality of the investment or the metal casting process.
- Solution: Use finer grain investment materials and ensure the slurry and stucco coatings are applied uniformly. Also, the pouring temperature and speed of the molten metal should be controlled to reduce turbulence and splashing.
6. Dimensional Inaccuracies:
- Problem: Finished parts may not meet the required dimensions, which can occur from improper mold-making or metal-casting variables.
- Solution: Utilize precise and calibrated measuring tools during the mold-making process. Regularly calibrate 3D printers if used for wax model production. Use simulation software to predict and compensate for metal shrinkage and other casting dynamics.
7. Defects from Contaminated Materials:
- Problem: Impurities in the wax, investment, or metal can lead to inclusions, spots, or weak areas in the cast.
- Solution: Always use high-quality, clean materials for every step of the process. Filter molten metal before pouring to remove any impurities or slag.
By anticipating these common issues and implementing the respective solutions, you can significantly enhance the quality and reliability of parts produced via lost wax casting. This not only ensures that your prototypes meet the necessary specifications but also reduces the need for costly reworks or adjustments in later stages of product development.
Advantages of Lost Wax Casting for Prototypes
Lost wax casting, also known as investment casting, is a favored method among engineers and designers for creating complex and intricate prototypes. This ancient technique has been adapted for modern manufacturing, offering unparalleled precision and versatility. Here, we discuss the distinct advantages of using lost wax casting for prototypes, especially when compared to other prototyping techniques.
1. High Precision and Detail:
Lost wax casting is renowned for its ability to produce components with extremely fine details and complex geometries that other methods might struggle to achieve. The precision of this process allows for the replication of intricate features, including undercuts and hollow sections, without compromising on the accuracy of the prototype.
2. Versatility in Material Selection:
Unlike some prototyping techniques that are limited to specific materials, lost wax casting can be performed with a wide range of metals, including aluminum, bronze, steel, and precious metals. This flexibility allows designers to experiment with different materials in the prototyping phase and select the one that best suits their final application.
3. Smooth Surface Finish:
Prototypes produced through lost wax casting typically have a smoother finish than those made through methods like sand casting or direct metal laser sintering (DMLS). This reduces the amount of post-processing work required to polish or finish the prototype, speeding up the overall production process.
4. Strength and Durability:
Prototypes created using lost wax casting benefit from the properties of the metal used, resulting in parts that are strong and durable. This makes the process ideal for functional testing where the prototype must endure operational stresses similar to those the final product will face.
5. Cost-Effectiveness for Small Batches:
For small to medium production runs, lost wax casting is more cost-effective than other manufacturing techniques, such as die casting or milling. The initial setup and tooling costs are relatively low, and the per-unit cost can be very competitive, particularly when considering the minimal waste produced during the process.
6. Efficiency and Waste Reduction:
Lost wax casting is an efficient process that minimizes material waste. Since the wax model can be reused and recycled, it supports a more sustainable manufacturing approach. Additionally, the precision of the process often eliminates the need for extensive machining or fabrication afterward.
Conclusion
The lost wax casting method, with its meticulous and systematic approach, remains a cornerstone in the field of precision casting and prototyping. By following the detailed steps involved—from designing the prototype to the final finishing touches—designers and engineers can leverage this age-old technique to produce intricate and precise components.
Recap of the Process:
- Designing the Prototype: Start with a detailed design, considering all aspects of manufacturability and the intricacies that can be achieved through casting.
- Model Creation: Utilize methods like sculpting or 3D printing to create a wax model that captures every nuance of the original design.
- Creating the Mold: Invest the wax model in a ceramic shell or other investment material, ensuring a flawless surface for casting.
- Wax Removal: Employ the lost wax process to melt and remove the wax, leaving a hollow cavity within the mold.
- Casting the Metal: Carefully pour molten metal into the mold, adhering to considerations specific to the metal used.
- Finishing the Prototype: Break away the investment mold, clean, and finish the metal prototype to achieve the desired quality and aesthetics.
- Inspection and Quality Control: Conduct thorough checks to ensure the prototype meets all specifications and quality standards.
Encouragement for Innovation:
Lost wax casting not only supports the creation of complex and precise prototypes but also encourages innovation in design and material use. This method offers a unique blend of artistic freedom and technical rigor, making it ideal for experimenting with new ideas and pushing the boundaries of what can be achieved in metal casting.
By integrating modern technologies and materials with this traditional method, practitioners can explore new possibilities and enhance the capabilities of their prototypes. Whether you are a seasoned engineer or a newcomer to the field of prototyping, the lost wax process offers ample opportunities to innovate and refine your craft.
Embrace the challenges and rewards of lost wax casting, and you may find that this time-tested method not only meets but exceeds your prototyping needs, enabling the creation of truly remarkable and functional products.
Further Resources
For those interested in deepening their understanding of the lost wax casting process and improving their practical skills, the following resources provide valuable information, tutorials, and opportunities for hands-on learning.
Reading Materials:
"Practical Casting: A Studio Reference" by Tim McCreight: This book offers a comprehensive guide to various casting methods, including lost wax casting, with detailed illustrations and step-by-step instructions.
"The Complete Metalsmith: An Illustrated Handbook" by Tim McCreight: While it covers a broad range of metalworking techniques, this handbook includes useful sections on casting that can enhance your understanding of the lost wax process.
"Jewelry Concepts and Technology" by Oppi Untracht: For those particularly interested in jewelry, this book delves into complex casting techniques, providing a thorough background on the lost wax method.
Online Tutorials and Videos:
YouTube – RioGrande's Channel: They offer multiple tutorials on lost wax casting, focusing on both the basics for beginners and advanced techniques.
Instructables (www.instructables.com): Search for lost wax casting projects where members share their step-by-step process and tips.
The Crucible's website (www.thecrucible.org): This educational facility offers online resources and video tutorials that cover various aspects of metal casting, including the lost wax method.
Courses and Workshops:
The Crucible (Oakland, CA): Known for its quality in arts education, The Crucible offers workshops on metal casting that include hands-on training in lost wax casting.
GIA (Gemological Institute of America): GIA offers jewelry-making and design courses that often include training in casting techniques. Check their course listings for specific details related to lost wax casting.
Local Art Centers and Community Colleges: Many local institutions offer continuing education classes in metalworking and jewelry making. These classes can be a great introduction to lost wax casting and other metal casting techniques.
Professional Associations:
The American Craft Council (craftcouncil.org): Membership can provide networking opportunities, access to conferences, and educational resources that include workshops and seminars on casting techniques.
The Society of North American Goldsmiths (www.snagmetalsmith.org): This organization provides resources, networking, and professional development opportunities for those interested in the craft of goldsmithing and metal casting.
Exploring these resources will help you gain a deeper understanding of the lost wax casting process and enhance your skills through practical experience. Whether you are a hobbyist looking to get started or a professional aiming to refine your technique, there is a wealth of information available to support your journey in mastering this ancient yet continually evolving art form.
© 2025 ScienceTimes.com All rights reserved. Do not reproduce without permission. The window to the world of Science Times.