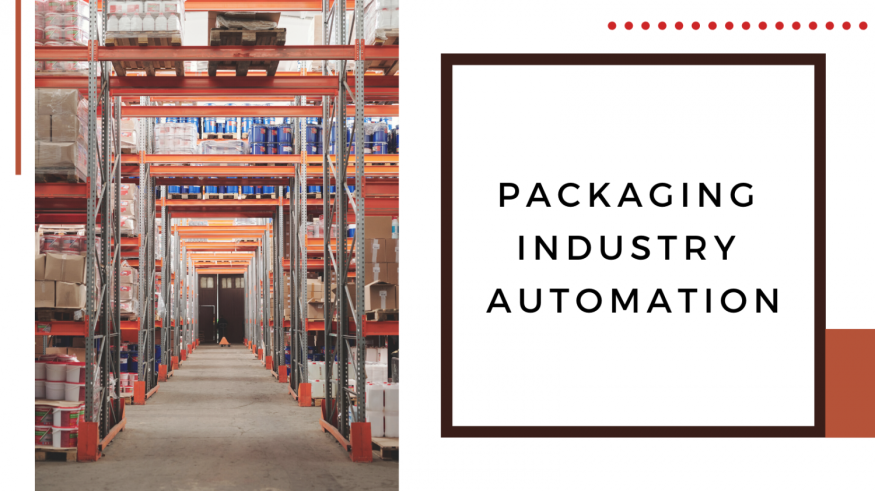
Linear actuators have found their special niche in the packaging industry. They have replaced the majority of pneumatic solutions because they:
Provide the movement precision that cannot be provided by other actuator types;
They are safe, you don't need to worry about leakages that are dangerous to the environment and might pose a danger to human health and even life;
The cycle times are faster;
They are easy to program and to control;
The positioning accuracy is very high;
The life cycle is longer;
The operation is clean;
The noise level by the operation is low;
The repeatability level is high.
All these features of a small linear actuator working from electricity are perfect for the packaging industry. Add low or absent maintenance costs, and you will not want to look for something else.
Application Types of Linear Actuators
In the packaging industry, many things shall be handled. Different size and shape products have to be handled. Different types of containers, such as boxes, bags, bottles, have to be managed. Many packaging variations have to be accommodated. However, it shall be done without applying a new machine every time you have a new packaging type.
The application of a mini linear actuator allows managing all the above mentioned challenges. Machines that use linear actuators are distinguished by increased accuracy and adaptability. Thus, they can cover the majority of needs. It, in turn, results in an increase of work efficiency. It happens because there are no delays and expenses connected with the purchase and setting up a new machine. Linear actuators are used in the following machines:
Box packaging machines: box packaging is believed to be a simple procedure. However, it also requires some variety. The box sizes and shapes can be different. A mechanism for box packaging with linear actuators allows handling those variations.
Filling machines: these machines use nozzles of different shapes and sizes. These nozzles are moved by a linear actuator mechanism. Actuators are fully enclosed. Thus, their application allows eliminating any risks of contamination.
Pick and place machines: here, multi-axis linear solutions are used. They can be applied for small or bigger components. Linear actuators are combined with rail guides and motors of the needed power. They have the needed stiffness level that is important for pick and place activities.
Labeling systems: electric actuators move the conveyor with products. A special optical detection system generates a signal that enables the label gun. It places the label in the needed position.
Linear actuators are used also for de-blistering mechanisms, palletizing systems, bags unclutter and inserters, loading systems, and similar. Now, you can hardly find a packaging system that doesn't use linear actuators. They provide the requested speed, the accuracy of movement and positioning, reliability, and easiness in management.
How to Choose a Linear Actuator for Your Packaging Application
The choice of a linear actuator depends on many factors. Of course, the budget is one of the main factors that will make an impact on your decision. However, there are some technical features that shall be considered, too. The most significant of them are as follows.
Precision Level
Check what level of precision is needed for your system. The majority of applications are ok with a 50 μm precision level. Thus, you can count on this value with the majority of actuators manufactured for the packaging industry. However, in some cases, a higher precision level is required. Also, check whether the repeatability and the accuracy levels are ok for your specific application.
Load Capacity
Load capacity is one more crucial feature to consider. Here, the range varies greatly. For heavy-duty systems of packaging and product handling, you need powerful actuators. Check the loads that the actuator manages during the acceleration and the high speed. In the technical specifications, check such parameters as thrust capacity, bending moments, dynamic load capacity. Some actuators are very powerful at low speeds but at high speeds, they can manage only reduced loads.
Travel Length
Here, you need to calculate the length at which the actuator shall move plus the space required to fit the entire system. In some cases, building a gantry system out of several actuators makes more sense than deploying, say, a robot.
Speed and Acceleration
Different actuators types have different speed, acceleration, and deceleration values. These values are important. For example, if your system needs to match the speed of a conveyor, you might need a faster actuator. For example, consider it if your robot hand needs to pick up a product, to place it in a different position, and then, to turn back for another product.
Final Thoughts
Linear actuators provide the packaging industry with all the required features. They are able to handle heavy loads, to provide the top accuracy level of positioning and movement, and the maintenance is almost not needed. It is expected that in the future, the application of electric actuators in the packaging and related industries will expand.
© 2025 ScienceTimes.com All rights reserved. Do not reproduce without permission. The window to the world of Science Times.