Material scientists Christopher Bates and Michael Chabinyc of UC Santa Barbara have teamed up to create the first 3D-printable "bottlebrush" elastomer. Along with the two postdoctoral researchers who played a key role in making the material, Renxuan Xie and Sanjoy Mukherjee, the team published their study in the journal Science Advances.
According to Phys.org, this resulted in printed objects that are ultra-soft and elastic that have mechanical properties resembling the human tissue.
Unlike the conventional elastomers, like rubbers that are stiffer, bottlebrush polymer is extremely soft elastomers because they have additional polymers that are attached to the linear backbone making it look like the bottle brush structure usually found in the kitchen.
3D printing the bottlebrush elastomer can be used in applications that need careful control over the dimensions of objects, such as actuators, sensors, and touchpads.
3D Printing the Ultra Soft, Elastic Objects
At the nanometer length scale, the material discovered by Xie and Mukherjee is said to involve the self-assembly of bottlebrush that creates a solid-to-liquid transition due to the applied pressure. That means this material is categorized as a yield-stress fluid for its property that makes it semi-soft fluid.
An example is a butter or toothpaste. Noticed how these soft solids could become liquids when squeezed through a syringe. The team uses this mechanical property to develop the ink they used for the 3D printing process they called direct ink writing (DIW).
Moreover, the flow of the material could be controlled depending on the amount of pressure applied to it to match the desired processing conditions.
"For instance, maybe you want the polymer to hold its shape under a different level of stress, such as when vibration is present," says Xie. "Our material can hold its shape for hours. That's important because if the material sags during printing, the printed part will have poor structural stability."
After 3D-printing the object, it is shined under UV light to activate the crosslinkers, discovered by Mukherjee, that link up nearby bottlebrush polymers, resulting in a super soft elastomer. Under any amount of pressure, this material can no longer be liquified as it permanently becomes solid that exhibits extraordinary properties.
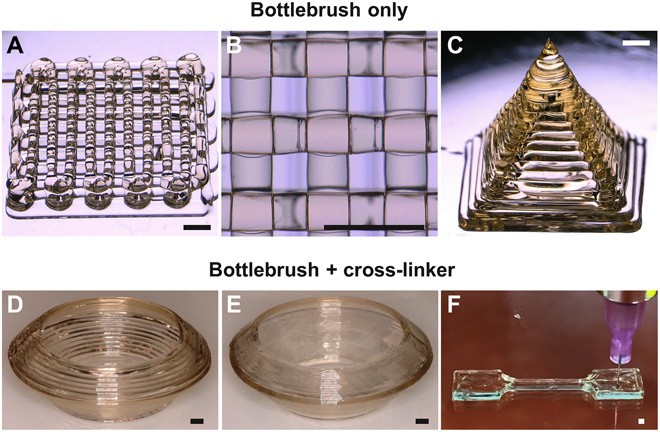
Room temperature 3D printing of super-soft and solvent-free elastomers
A Serendipitous Event: Scientist Accidentally Discovers Ink
Mukherjee was developing another material for a project at that time when he accidentally discovered the material, Science Daily reported. He found that the material he accidentally made increased the amount of charge that can be stored by an actuator and knew immediately that this material was special.
Bates said that upon seeing the material, it dawned to them all that they could 3D-print it which is cool because there are no 3D printable materials yet that are as soft as this new material.
He added that advances in chemistry have made it possible for bottlebrush polymers to be recognized in the field over the past ten years.
"These super-soft elastomers might be applicable as implants," Bates said. "You may be able to reduce inflammation and rejection by the body if the mechanical properties of an implant match native tissue."
Furthermore, the researchers noted that the new material is pure polymer, which means that water or solvent is not needed to 3D-print the objects. Usually, when 3D-printing, the solvent is added to the ink to liquefy it. That is why the objects made with this accidental ink are super soft and elastic that resembles human tissue.
RELATED TOPIC : Research on Electrolysis Leads to a More Environmentally Friendly Way of Producing Cement
Check out more news and information on Material Science on Science Times.
© 2025 ScienceTimes.com All rights reserved. Do not reproduce without permission. The window to the world of Science Times.